Ahead of Schedule
- ConnexFM
- Oct 31, 2022
- 4 min read
Updated: Nov 1, 2022

All facilities managers should implement an extensive preventative maintenance program.
By Amelia Bridgford
There’s a reason most people are still familiar with Benjamin Franklin’s famous proverb: “An ounce of prevention is worth a pound of cure.” It applies to nearly everything, from personal health and wellness to automotive care. Many facilities managers make this sensible advice a tentpole of their managerial philosophy in the form of a solid preventative maintenance program. Still others rely on a break/fix model of addressing problems as they arise. When it comes to preventative maintenance, what are the industry trends, and what costs are associated with each style of management?

Consider the Costs
When tasked with maintaining multi-site facilities, most decisions boil down to one basic consideration: how will this impact the bottom line? What sounds like a simple equation rarely is, particularly in a modern era complicated by the increasing popularity of online commerce, rising real estate costs and, of course, a global pandemic. When margins are tight and costs must be cut wherever possible, it may not be easy to justify the expense of preventative maintenance in a facility that is running smoothly. “When it comes to preventative maintenance, there is a substantial cost, that’s true,” said Michael Gersh, National Account Executive for SLM – Facility Solutions Nationwide, a facilities management organization specializing in 30-plus trades across all 50 states. “But how does it compare to the cost of being forced to shut down your operation when a critical piece of equipment fails?” Indeed, there may be no more important cost-benefit analysis for a facilities manager.
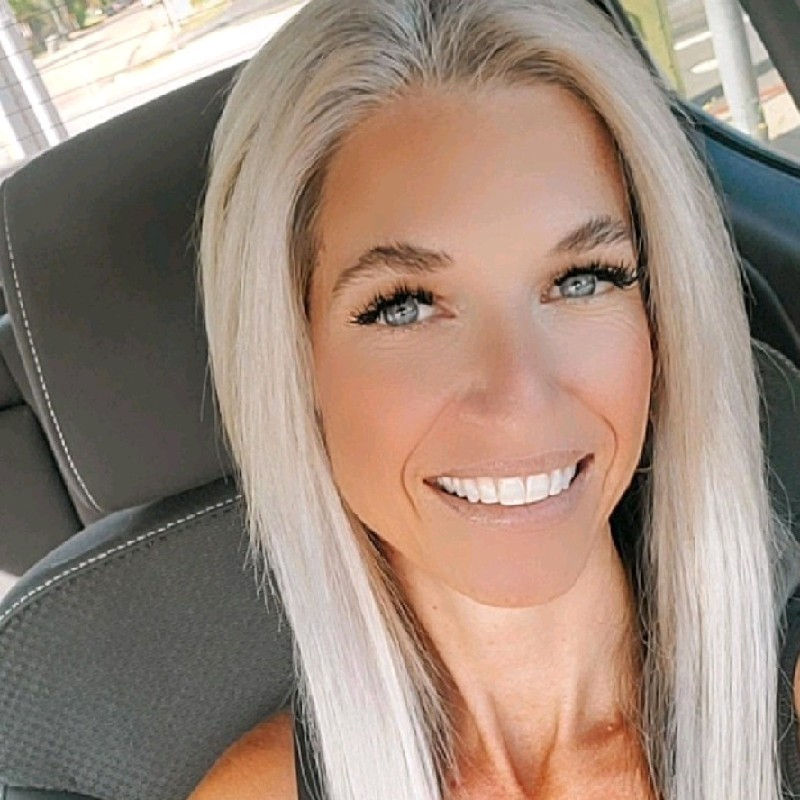
Shannon Markwell, Acquisition Facilities Manager for Public Storage, agrees that a proactive approach to maintenance is wise. “It’s definitely a cost savings in the long run if you’re strategic in your implementation,” she said. “But you’ve got to do your due diligence — know your inventory, run the numbers, get all the information in front of you so you can make an informed plan.”
Putting Preventative Maintenance into Practice
When it comes to the best way to build and implement a preventative maintenance program, both Gersh and Markwell recommended taking a detailed inventory of the assets in your facilities as a starting point. How old are the units in each facility? When was the last time they were serviced, and the last time they malfunctioned? Flag the older and more problematic units first and focus your initial attention there.
“You’re going to want to understand what you’ve got out there and be strategic rather than just doing the same maintenance for every store across the fleet,” Markwell explained.
Environmental conditions should also be considered. “You have to look at the climate in a given location,” Gersh added. “For example, in dry, desert areas where there is a lot of dust in the air, filters are going to need to be changed more often.”
A Chilling Example
To illustrate the value of a solid preventative maintenance plan, let’s look at one of the biggest troublemakers in facilities management: heating and cooling systems.
“I don’t care where you’re located — it could be the Northeast or the Southwest — if your HVAC goes down, you’re in trouble,” Markwell cautioned. “No cool air, no warm air — either could keep you from operating properly. And while you’re waiting to get those parts or get a unit replaced, you’re down the entire time.” Replacing or repairing units in an urgent situation also forces a company to settle for what is available immediately and can be installed quickly, limiting their ability to price shop and find equipment with the best value.
Heating and cooling aren’t just about comfort — they can also be critical to safeguarding a quality product. “Imagine you’re running a 4-star steakhouse and you lose refrigeration completely,” Gersh said. “You might have thousands of dollars of meat and produce unusable in a matter of hours. It’s not just the sales you’d lose in a day that you’re forced to close, it’s your backstock product, as well.”
A guiding principle in maintenance appears to be this: whenever possible, catch things early before a problem becomes an emergency. “Take care of the simple things, because the simple things eventually become complicated and expensive if they aren’t handled,” Markwell advised. “And a trained technician doing preventative maintenance will catch a fan or a belt that’s starting to fail, resolving the situation before it causes a big problem.”
Gersh agreed and added that a proactive approach to maintenance is not only good for the health of equipment, but for the entire company. “If you maintain your equipment and make sure that it’s functioning properly, it’s only going to help your business run better and more efficiently,” he said.
Facilities managers looking to transition away from a more reactive maintenance strategy are not alone. The challenges brought by the pandemic are causing many in facilities management to reconsider their approach to maintenance, a trend Gersh is now seeing every day. “COVID-19 forced people to look at their equipment and assets and make sure that they’re running optimally, properly and safely,” he said. “There isn’t as much room for error, and more and more people are looking to take care of what they’ve got. And I think that’s ultimately a good thing.”
Comentarios