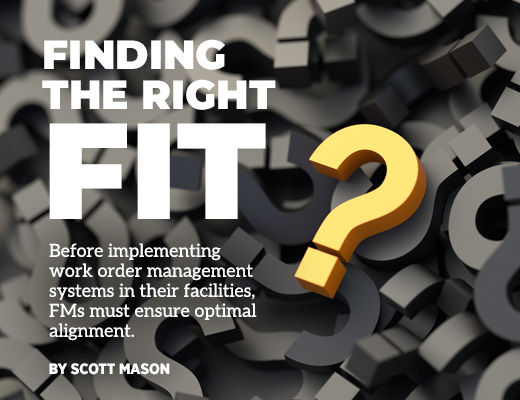
Before implementing work order management systems in their facilities, FMs must ensure optimal alignment.
By Scott Mason
In the complex ecosystem of multi-site facilities management, efficiency and coordination are paramount. Central to achieving these goals is the adoption of robust work order (WO) management systems. These systems, designed to streamline the process of maintaining and repairing facilities across various locations, are critical tools in the arsenal of any facilities manager. By automating the creation, assignment, tracking and completion of work orders, these systems ensure that all maintenance tasks are addressed promptly and effectively.
WO management systems serve as a vital communication bridge between maintenance teams, facilities managers and other stakeholders. They allow for real-time updates, centralized data storage and detailed reporting, which facilitates decision-making and operational transparency. Moreover, they help prioritize tasks based on urgency and impact, ensuring that resources are allocated appropriately and maintenance backlogs are minimized.
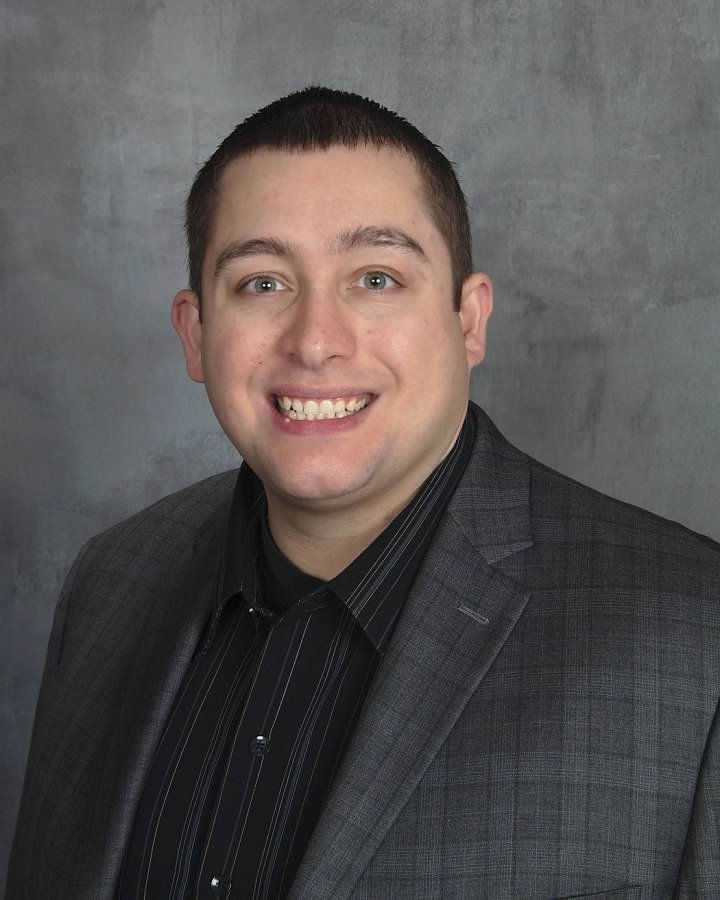
The importance of these systems cannot be overstated. Joseph Williams, Facilities Manager at Five Guys, said WO management systems are essential to the operations of his department. “It's vital for data analytics and doing more with less, especially as departmental headcount issues continue,” he said. “Cost constraints that FM departments face require doing more with less on the capital expenditure side, as well.”
Prime Partners and Due Diligence
Maintaining consistency in practices and standards is challenging for organizations with multiple geographical locations. WO management systems foster uniformity, enhance asset lifespan, optimize labor utilization and reduce costs.
However, a proper supplier partner is essential to ensure this all happens harmoniously.
All facilities differ, meaning one organization’s WO management needs may differ from the next — even if they’re in the same industry. A savvy FM must ask any vendor the right questions to ensure the proper fit. You don’t want to be the FM who didn’t do their due diligence and get locked into a long-term contract for a solution that doesn’t work for your company.
Williams shared a few considerations FMs should always ask or think about before selecting a partner or system.
Preventive Maintenance: FMs should always request a detailed demonstration and knowledge about a particular solution’s preventive maintenance module, Williams said. “If the preventive maintenance plan is clunky or difficult to set up in the software, that will lead to a series of problems down the line.”
Stakeholder Engagement: A common mistake is not identifying and consulting with the other departments and teams who will also be working in the new system before moving forward. “Not including the accounting or operations team in the process is a big mistake,” Williams said. Gather these people internally, gauge their wants and needs and verify that the WO management system vendor can fulfill them.
Training: Implementing a new technology solution must be seen through the lens of change management procedures, and one of the most important things to consider is proper training. “What kind of initial or ongoing training does the vendor provide for their system?” Williams asked.
Not only is training important for an organization’s internal employees, but FMs must think about any outside service contractors who may need to operate within the system as they perform tasks. “People change jobs within the service company organizations, and there's not a lot of knowledge transfer,” Williams said. “And depending on the organization, you might not have the bandwidth to retrain the same vendors. So, you need to ask what kind of services or offerings they provide to keep your service companies updated with the latest and greatest information or training resources.”
System Integration: FMs would be wise to ensure that their existing technology solutions synchronize well with whichever WO management system is selected, with the most important task being data importation and alignment. Ask any vendor about the legacy data input process and set aside time to make sure your team does this properly. “If you aren’t willing to put in the time upfront, you're not going to get the best data output in three to five years, which is ultimately the goal of these systems,” Williams said. “If your data doesn’t initially align, you’ll be looking at a one- to three-year clean-up process. It’s time and resources that you just don’t have.”
Sharing Knowledge
Williams also stressed the importance of connecting with peers in the facilities industry for tips on how to best to run your WO management system. Notably, Five Guys’ current partner sets up a time for all of their clients to get together and brainstorm how to improve the product and share best practices for using the system.
“You can obtain an incredible amount of knowledge of what other people are doing and can achieve with the program,” he said. “Check with the potential vendor to see if they offer outreach or are willing to share who their current customers are. This is especially important when you're looking at initial systems.”
Comments